Streamlining Operations: A Case Study on Production Planning at ABC Manufacturing
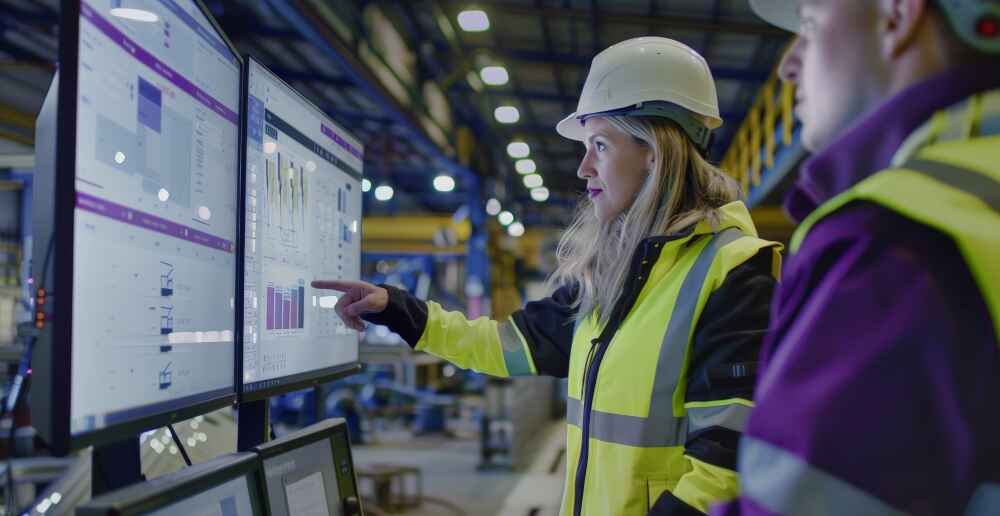
Introduction: ABC Manufacturing, a leading player in the automotive components industry, undertook a strategic initiative to optimize its production planning processes. This case study delves into how the company redefined its approach to production planning, addressing challenges, improving efficiency, and ensuring a synchronized supply chain.
Background: ABC Manufacturing faced challenges in meeting production targets, managing resources efficiently, and minimizing lead times. Recognizing the need for a robust production planning strategy, the company initiated changes to enhance overall operational effectiveness.
Objective: This case study aims to explore how ABC Manufacturing implemented production planning strategies, the impact on operational efficiency, and the lessons learned during the process. Three key questions have been formulated to delve into the company's experiences and extract valuable insights for businesses navigating complex production planning scenarios.
Challenges Faced:
Resource Allocation and Utilization:
ABC Manufacturing struggled with optimal resource allocation, leading to inefficiencies in workforce utilization and equipment downtime.
Lead Time Reduction:
Lengthy lead times affected the company's ability to respond quickly to market demands and capitalize on business opportunities.
Supply Chain Synchronization:
The lack of synchronization between production planning and the broader supply chain impacted inventory levels and order fulfilment.
Conclusion: The ABC Manufacturing case study underscores the critical role of effective production planning in optimizing operational efficiency and competitiveness. The questions posed aim to extract practical lessons and strategies that can benefit other businesses seeking to enhance their production planning processes in dynamic manufacturing environments.
Learning Objectives
1. How did ABC Manufacturing address challenges in resource allocation and enhance workforce and equipment utilization through its production planning strategies? What specific measures were implemented to optimize resource allocation?
2. In what ways did ABC Manufacturing reduce lead times and improve responsiveness to market demands through changes in its production planning approach, and how did this impact the company's competitive position?
3. How did ABC Manufacturing synchronize production planning with the broader supply chain to address inventory challenges and improve order fulfilment, and what lessons can be drawn for other manufacturers aiming to optimize supply chain coordination?
Leave a Reply
Your email address will not be published. Required fields are marked *
0 Replies to "Streamlining Operations: A Case Study on Production Planning at ABC Manufacturing"